If you own a business in Sydney or are involved in the supply chains of anything from construction, renovation and automotive to aerospace, civil engineering and general manufacturing, some fabrication processes and terms can seem confusing. Even today, the most obvious terms can cause confusion. ‘Welding’ and ‘fabrication’ sometimes do.
We always assume that not every decision-maker is a highly experienced fabrication line manager or shop floor supervisor. In some instances, we’ve seen accountants, sales managers and even business development managers in charge of metal fabrication projects in Sydney.
So, let’s explore the difference between welding and fabrication and drill down further into the derivatives of each.
So, what is the difference?
The best way to explain this is as follows: fabrication is the overall process of manufacturing metal, whereas welding is one single part of the fabricating process. Fabrication may include welding, but welding is always a part of fabrication. In a metaphoric sense, if fabrication can be likened to a finished cake, then welding can be viewed as one of the components of the finished item, such as flour.
While welding is basically a single process, fabrication can be a single process, but more often than not it is a combination of processes and can include welding, cutting, assembling, grinding, and bending, to name a few.
And you likely know from experience across projects that metal fabrication can be subdivided even further into more specialised sub-groups. For example, you may have a more specific stainless steel or aluminium fabrication project in Sydney. Each process may require specific steps depending on the final outcome requirement, including the use of different types of PPE for different fabrication processes.
Why is it important to understand the basics of welding?
Welding is, without doubt, the most common process in fabrication with origins that can be traced back 2,000 years to the bronze age. But it’s modern-day Australia where welding, its Quality Standards, and its place in fabrication is important to many industries. So, let’s examine what it does in practice.
How it works
Welding joins materials, usually metals or thermoplastics, by using high heat to melt the parts together and allowing them to cool, causing fusion. It is completely different to lower-temperature techniques such as brazing and soldering which do not melt the base metal. The bond formed is very, very strong. This is why it is so prevalent in the majority of fabrication jobs your company is likely to do.
Why we weld
Compared to fixtures such as screws and nuts/bolts, welding gives the ultimate bond between metal items, so when your job specifications demand this high level of outcome, you know you have to choose the right welding option and ensure it is done 100% correctly.
Certification
Much like any other industrial discipline, welding does have its accountability. Especially if your projects are outsourced, our advice is to check the company or individual used in the welding process is properly certified. At the very least they should show evidence of a Certificate III in Engineering – Fabrication Trade.
Errors can be costly
Certification is a great indicator that the welder understands the correct procedure. Errors are costly and come in many forms such as slag inclusions, porous work, undercuts, weld cracks, incomplete fusion, incomplete penetration, spatter and more. Welding that is rejected can be extremely costly to repair or replace. Get advice if you have to, do not leave this to guesswork!
Different types of welding
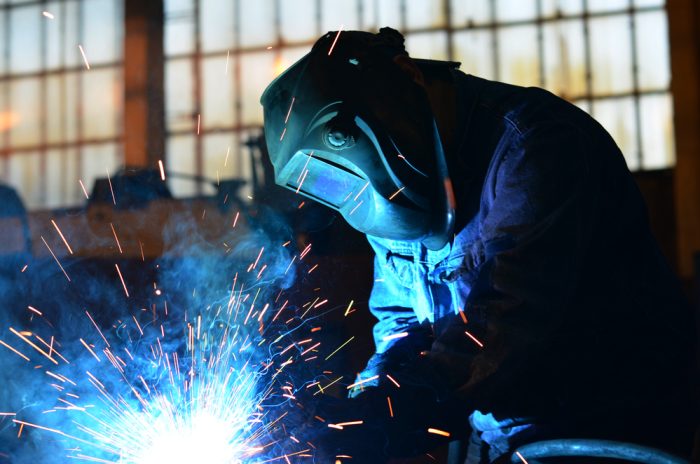
Now that we have identified the importance of welding in the overall scope of fabrication, it is worth keeping the following handy as it can help you understand the various types of welding. This will help work through challenges in your estimating.
Gas Metal Arc Welding (GMAW/MIG)
The process works when an electric arc forms between a consumable MIG wire electrode and the workpiece metal. This heats the workpiece metal causing them to melt and join. Both the wire electrode and a shielding gas feed through the welding gun, shielding the entire process from atmospheric contamination.
Gas Tungsten Arc Welding (GTAW/TIG)
This arc welding process uses a non-consumable tungsten electrode to produce the weld. An inert shielding gas protects the weld area and electrode from oxidation or other atmospheric contamination.
Shielded Metal Arc Welding (SMAW)
Shielded metal arc welding (SMAW) is also known as manual metal arc welding (or stick welding). It is a manual arc welding process that uses a consumable electrode covered with a flux to lay the weld.
Flux Cored Arc Welding (FCAW)
Flux-cored arc welding (FCAW) is a semi-automatic or automatic arc welding process using a continuously-fed consumable tubular electrode containing a flux in its core and a constant-voltage welding power supply.
Of course, one of the biggest challenges is finding welders to do the job. Weld Australia estimates a welder shortage of 70,000 welders by 2030 in the country. A specialised fabrication business should ideally have everything in place, so you don’t have to worry about finding one yourself.
Is fabrication different from manufacturing?
In simplistic terms, ‘manufacturing’ applies to consumer-level work while ‘fabrication’ applies to industrial work. But our view is there is a little more to it than that:
Fabrication is more or less an all-encompassing term that describes constructing products by combining parts or structures together. It works for different metals, although the steps involved in stainless steel fabrication may differ from how structural steel fabrication works. Aluminium and stainless steel fabrication also follow their own processes depending on the final purpose.
Conversely, manufacturing is the process of converting raw materials (commonly referred to as ‘blanks’) into a finished product normally using fairly large-scale industrial operations.
What processes are part of fabrication?
The more familiarity you have with the processes, the more accurate your job estimations and margins based on design standards will be. Processes range from very hands-on manual to highly sophisticated software-driven machinery processes. The processes may also depend on the choice of material, so it is important to understand the properties and uses of different metals. As an example, we have detailed the clear differences between mild steel and stainless steel and the specific applications for each type of metal. Once the metal is finalised, some of the most important processes in fabrication include:
Plasma cutting
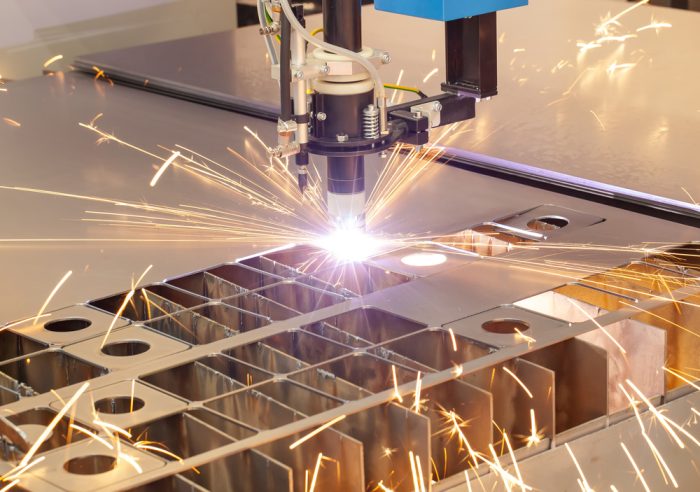
Plasma cutting is a process that cuts through electrically conductive materials by means of an accelerated jet of hot plasma. Typical materials cut with a plasma torch include steel, stainless steel, aluminium, brass and copper, although other conductive metals may be cut as well.
Drilling & tapping
Drilling refers to creating a smooth hole in a material with a drill and motor. Tapping is the action that creates a thread into the side of the hole.
Polishing
A finishing process that smooths the surface of a workpiece using an abrasive and a work wheel or a leather strop.
Machining
When a material (often metal) is cut to a desired final shape and size by a controlled material-removal process.
Bending
A manufacturing process that produces a V-shape, U-shape, or channel shape along a straight axis in ductile materials, most commonly sheet metal Often uses machinery including brake presses and pan presses.
Assembly
A manufacturing process in which parts are added to a product in a sequential manner.
Shearing
This process cuts stock without the formation of chips or the use of burning or melting (the common name for the process is die cutting).
Cutting
Common cutting processes include sawing, shaping (or planing), broaching, drilling, grinding, turning and milling.
Punch pressing
When a machine changes the size or shape of a piece of material, usually sheet metal, by applying pressure to a die in which the workpiece is held.
Quality is a key priority in metal fabrication, As such, there are specific quality control measures in metal fabrication to adhere to the project specifications and ensure a quality result.
Conclusion
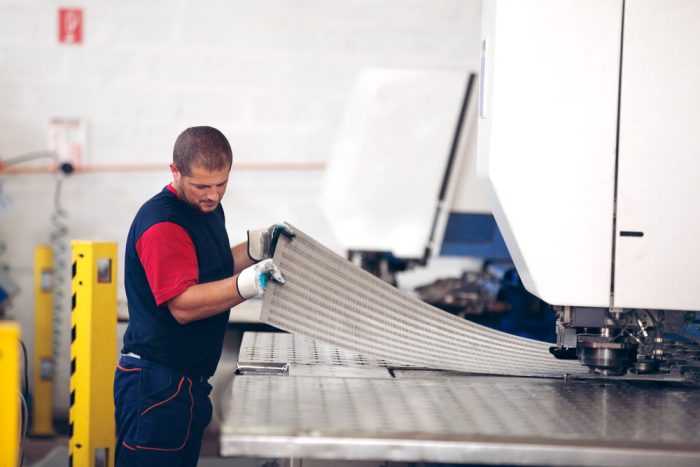
When it comes to welding or overall fabrication, you are not in the minority if you feel like you don’t know everything. Unless you have many years on the tools and working with the software running welding machines and most large fabrication machinery, there are bound to be things you don’t know. This is perfectly normal. Your skill may lean more towards managing the administrative side of a project or dealing at an executive level running what-if scenarios and planning schedules etc.
Avoid guesswork when choosing the right welding or fabrication process for your next project. Let the experienced fabrication team at Prime Fabrication help you.
Our services also include aluminium and stainless steel fabrication in Sydney.