Stainless steel is a durable and elegant metal used by many industries because of its resistance to corrosion and versatility. It sees use in architecture, food processing, aerospace and many other sectors, all of which depend on this useful metal. However, while stainless steel is a metal with properties that make it perfect for many uses, it can be complex to fabricate.
In this article, we will explore the processes that skilled metal fabricators use to mould and manipulate this metal into various components needed for modern life. They can bend, cut, shape, and join the material into the final product using different techniques.
Whether single items or large production runs, metal fabricators help you choose the right alloys and the best techniques to manufacture whatever you need. What steps do they use and how do they overcome the challenges of working with this metal?
What is Stainless Steel Fabrication Used For?

Before diving into the processes used to fabricate stainless steel, it is useful to know how and where the metal is used. Each use requires different processes to deliver the final product and maximise the benefits.
Due to its high structural strength, stainless steel often sees use in construction, especially for structures intended to resist rusting. Due to its beautiful finish and resistance to corrosion, metal is a common material for decorative and architectural features such as balustrades and window frames. But here, it is important to understand its differences from structural steel, which may have a higher carbon and iron content. An experienced fabricator will be able to clearly advise on how structural steel fabrication works compared to stainless steel, and which material is better suited to your application.
Stainless steel is heat resistant and can handle high stresses, making it useful for the aerospace and automotive industries, water vessels, and boilers. Its corrosion resistance and easy cleaning make it hygienic and optimal for kitchens, food production facilities, and surgical tools. Now, let’s look at the stages of stainless steel fabrication.
Steps Involved in Stainless Steel Fabrication
To break it down further, let’s try and understand the steps involved in stainless steel fabrication.
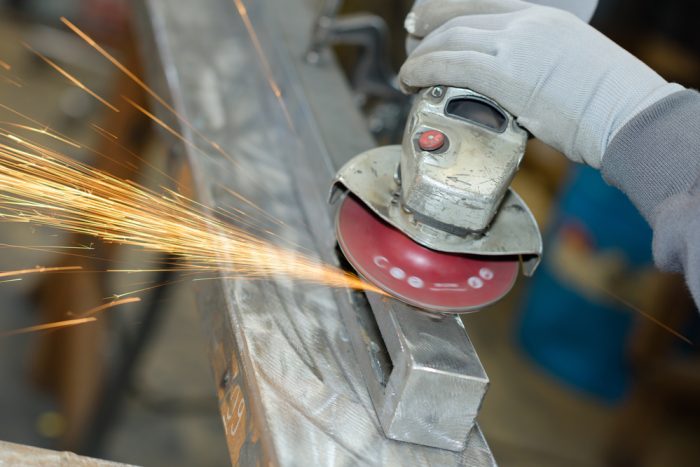
Step 1: Plan and Design
For any stainless steel project, the first stage involves understanding the requirements, careful planning and working out the best processes to use before getting started. A fabricator should ideally be able to give you an idea of which type of stainless steel best suits the job.
Different stainless steel alloys emphasise strength, corrosion resistance, welding, or hygiene properties. Other projects may focus on heat resistance or hardness, while some uses need a beautiful finish. It’s important to get the material right as there are some specific differences between different types of steel, such as the differences between mild steel and stainless steel – making each type suited to varied applications.
While there are many grades of stainless steel, the most common are:
- Grade 301: Malleable with an attractive finish, making it useful decorative work
- Grade 304: The most widely used, this grade offers high corrosion resistance and is easy to weld and form, making it the metal of choice for kitchens, medical facilities, bathrooms, and outdoors
- Grade 316: This type is highly resistant to corrosion, making it perfect for marine use, harsh environments, and surgical tools.
Once they have chosen the right grade, the fabricator can work on the metal, starting with the all-important preparation.
Step 2: Clean and Polish
This preparation stage is crucial for stainless steel fabrication because any flaws in the metal will lead to weaknesses and imperfections in the final product.
Shot Blasting
The first stage involves assessing the metal and using shot blasting to remove any surface impurities and rust.
Surface Preparation
Next, the fabricator will clean and prepare the surface before drawing on a variety of techniques for making the product.
Step 3: Fabrication
Working carefully to the design specs, the fabricator chooses the right techniques for the job, drawing upon the right tools to manipulate the steel carefully. Some fabrication techniques involve welding, cutting, bending, forming, blanking, punching and joining.
Cutting
Using various machines and tools, including shears, circular saws, and plasma torches, metal pieces are cut to the right dimensions, carefully smoothing any rough edges.
Bending and Forming
Fabricators use a variety of techniques to bend and shape stainless steel. They may hammer the metal into the right shape or form it using a jig or machine. For some fabrication, they may use rollers to bend the metal, especially for tubing.
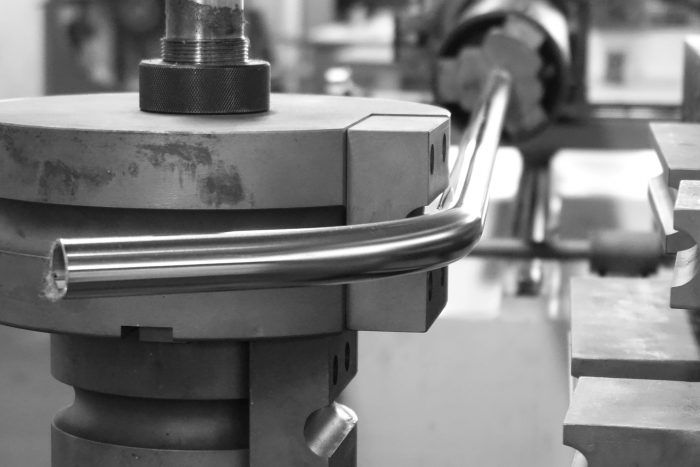
Blanking and Punching
Blanking the metal involves punching out the final part from a sheet with a die while piercing and punching press out excess material to leave the right shape. The fabricator may also nibble away excess metal from the edges, especially for irregular shapes.
Machining
Stainless steel sometimes uses machining to work the metal, including grinding or milling to remove excess metal and drilling to create holes.
Welding and Joining
A fabricator may weld multiple pieces together when they need to join the metal. This process draws on their specialised knowledge to avoid compromising the metal or damaging the surface. Other common joins use rivets, bolts, or crimping.
Step 4 – Finishing
Different uses of stainless steel require different finishes. The fabricator may use grinding, buffing, and polishing for a decorative finish to leave a shiny finish. For some components, they may even powder coat the metal for decorative purposes or for extra corrosion resistance.
Step 5 – Testing and Quality Assurance
With the part assembled and finished, the product moves to the final stage, where the fabricator tests it to ensure quality is up to high standards and that the assembled piece fits the specifications without showing any signs of weakness.
Checking Measurements
As part of the process, the measurements and checked against the design to ensure the part fits and is finished correctly. The part is also inspected to look for any imperfections on the surface.
Returning and Reworking
If the quality assurance checks reveal any problems, they return the part for reworking or reject it completely.
Advance Testing for Critical Components
For particularly critical parts, such as engine components or structural steel, the fabricators will use various additional tests to ensure there are no small faults or cracks.
Client Final Approval
Once the part passes the quality assurance check, the part is ready for the client’s final approval.
Why Use Prime Fabrication
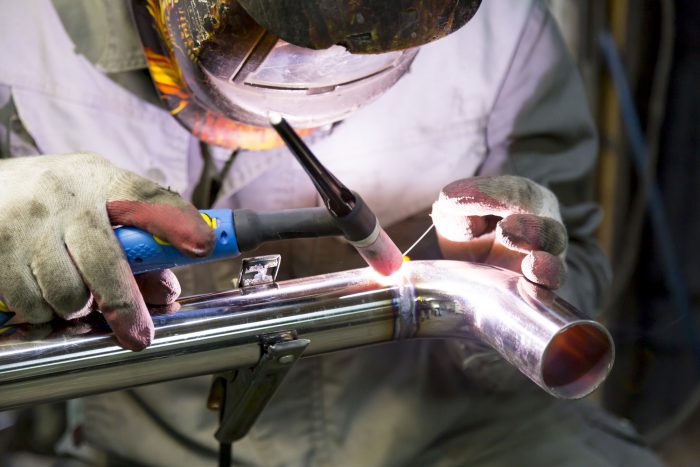
As you can see, stainless steel, while an exceptionally useful metal, needs a careful touch when fabricating it into a component. Prime Fabrication is a metal fabricator with years of experience working with all grades of stainless steel. If you need metal fabrication in Sydney, We know exactly what processes to use and what grade of stainless steel suits a project.
Because we have a range of tried-and-tested processes, we can offer competitive quotes for all jobs, large or small. With knowledge of the specialised techniques needed for all industrial sectors and the ability to work offsite or offsite, we can help whether you need a single product or a full production run.
If you want to find out how we can help, contact us for a quote and discuss your project.